Hello and Welcome Morpheus0101
Hello and very
Morpheus!
Wow, thanks...what a way to make a "Debut" here!...Welcome aboard
I am very glad you read my first thread...as it unfolds the Fundamentals to understand this Machines, and much more...
Yes, we needed Arduino Codes Experts...as Dana was going crazy with all He was doing...
Many thanks for your contributions...We, will help you as much as you need in building your Machines, my friend.
I saw video, looks awesome...
One thing I noticed...and may be that way...When you started accelerating the sequences, I noticed LED's went dimmer...to almost faded out...that does not means signal is also getting weaker right?
Anyways...with this set up we have here, is so flexible and upgradable and enhanced...that we will not have any problems at all...
Now, the excitement will come...when you guys see, how those small LED's could drive much faster the Real Vortex at Rotors...
...while they go just "cruising" at Mid speed...
Eventually... We are arriving to our "Final Destination" point...We have an awesome Monster Pulser...built by Sir John Stone...that has been proven beyond doubt to be able to handle the fast and high spikes from Radiant...awesome work John!...and I hope everything is well at home.
We have heck of replications going on now...and I know -at least I am- waiting to see those Machines ran by the Off Pulses...
Regards and Thanks again Morpheus0101
Ufopolitics
Originally posted by Morpheus0101
View Post
Hello and very
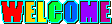
Wow, thanks...what a way to make a "Debut" here!...Welcome aboard
I am very glad you read my first thread...as it unfolds the Fundamentals to understand this Machines, and much more...
Yes, we needed Arduino Codes Experts...as Dana was going crazy with all He was doing...
Many thanks for your contributions...We, will help you as much as you need in building your Machines, my friend.
I saw video, looks awesome...

One thing I noticed...and may be that way...When you started accelerating the sequences, I noticed LED's went dimmer...to almost faded out...that does not means signal is also getting weaker right?
Anyways...with this set up we have here, is so flexible and upgradable and enhanced...that we will not have any problems at all...
Now, the excitement will come...when you guys see, how those small LED's could drive much faster the Real Vortex at Rotors...

Eventually... We are arriving to our "Final Destination" point...We have an awesome Monster Pulser...built by Sir John Stone...that has been proven beyond doubt to be able to handle the fast and high spikes from Radiant...awesome work John!...and I hope everything is well at home.
We have heck of replications going on now...and I know -at least I am- waiting to see those Machines ran by the Off Pulses...

Regards and Thanks again Morpheus0101
Ufopolitics
Comment