Update on the 3/4 inch build
Well, my 27 millimeter cutters arrived, and so I was able to complete the bore hole drillings on the two 1/4 inch thick hardboard wheels. I'll show this process from layout to completion in case anyone else would like to do a small build. I purchased a 2-foot by 2 foot piece of 1/4 inch thick hardboard at Home Depot, which worked out nicely. The panel was actually about 1/4 inch larger in both dimensions, and as I would be able to cut four 12-inch wheels from the panel, I decided to go with 12 inch circular wheels. The dodecagon wheel diameter for a 3 inch build was figured at 46.5 inches, so proportionately the 3/4 inch build would call for an 11.625 inch diameter. I could have built to that specification, but chose to go with 12 inches as it will only make the build more stable, since each pipe will have more wheel surface to lay upon. Here's a photo showing the means that I used for laying out the circles and their radian lines.
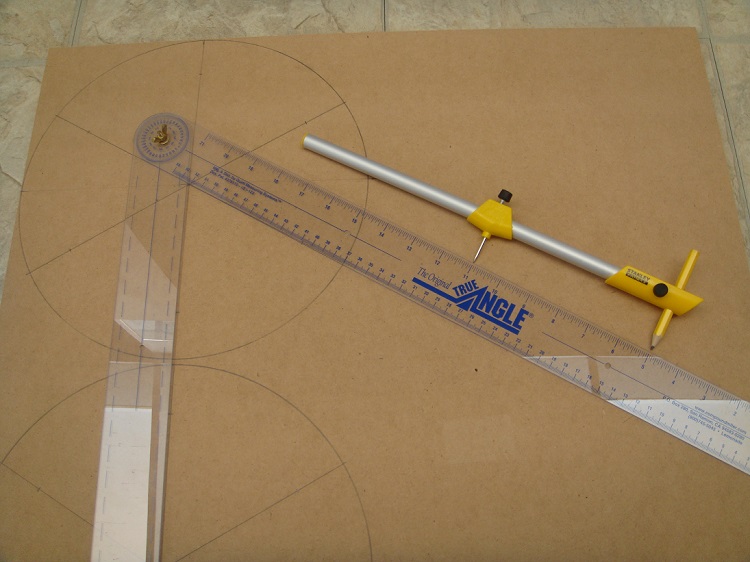
The circle scriiber is a Stanley Fatmax Chisel Compass, and works far better than an ordinary compass for drawing circles this size or larger.
The True Angle layout tool is a 23 inch model and allows for very accurate angle settings and scribing of the radian lines. Since two wheels are used for this build, the radian lines are scribed 60 degrees apart, and when assembled on an axle the wheels will be rotated for a 30 degree separation.
In the photo below, you can see that I scribed another smaller circle upon the wheel. The radius for this circle is 4.5 inches to be in proportion to build specs. The bore holes for the pipes will be centered where the smaller circle intersects the radian lines. I cut out the 12 inch wheels with a saber saw as I didn't have a jig saw available, which I would have preferred using. The idea is to cut close to the 12 inch circle's pencil mark without cutting into the mark. Next, I drilled a 1/8 inch hole at the wheel's center and followed that up with a 1/4 inch hole so that I could attach and secure a 1/4 x 3 inch round head stove bolt. Starting with the smaller drill allows for better accuracy in following the mark left by the chisel point compass. This allowed me to insert the bolt in a a drill chuck and spin the wheel so that I could true it by applying a sanding block to the perimeter as it rotated.
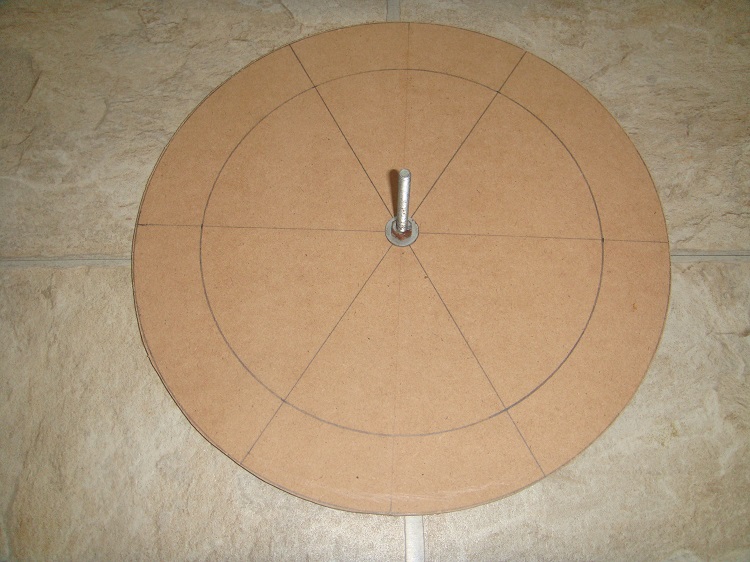
After truing the wheel, the last step was to drill the 27 millimeter bore holes which the pipes must pass through. I used an awl point to accurately make a depression at the centers where the smaller circle intersects the radian lines, and passed a 1/8 inch drill bit through those centers using my bench-top drill press. I then mounted the 27mm cutter in the drill chuck and carefully lined up the cutter's 1/4 inch center drill with each of the 1/8 inch holes. Here's what each of the completed wheels look like.
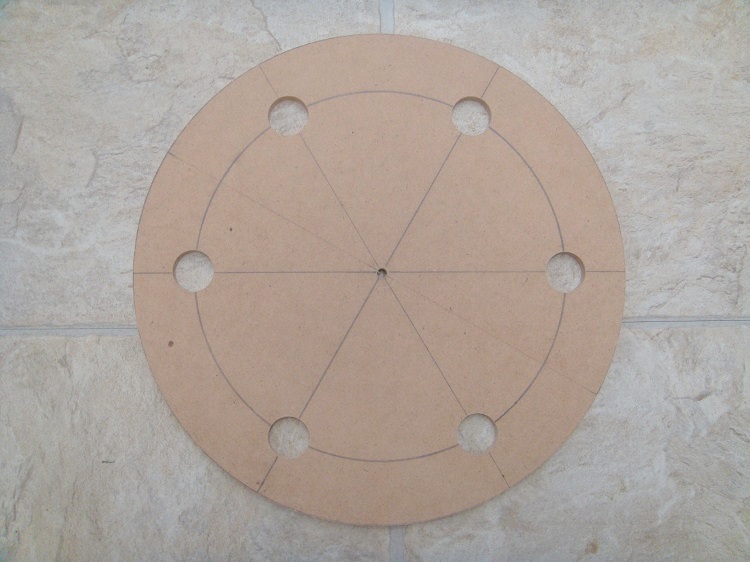
The work on the wheels is now completed, except that the center holes must be enlarged to accept the 3/8 inch x 6 inch shaft. To place the wheels the desired 1.250 inch distance apart, and lock them to the shaft so that they are set 30 degrees apart in rotation, I will be using shaft collars. The collars are attached to the shaft with set screws to lock them in place, and I will use a small drill to bore a hole through the side of each collar that will also pass through each wheel when in proper alignment. That will allow me to insert a small screw to lock the wheels to the collars. Two more collars will be placed further out towards the ends of the shafts, and these will be used to maintain the rotational plane at the center of the holding device. I haven't drawn up any plans yet for the holding device, but in my mind it would appear to be a wood block used as the base, with support arms extending upwards from the sides of the block. Nothing extravagant - just simple and supportive. The next step now is to assemble the pipes and fittings up to the 90 degree elbows, attach the short pipes to the elbows, pass these through the bore holes in the wheels, and secure the end caps. Since the elbows and end caps allow the pipe to be inserted 3/4 inch until it bottoms out, and since the wheels are 1/4 inch thick, this means that the short pipes which pass through the bore holes should be no more than 1.750 inches long. I prefer to actually finish them to slightly less than that so that when the end caps are cemented in place they will tightly sandwich the wheel surface between the end caps and the elbows so as to avoid any sideways play as the water sloshes about.
Here's a link where you can read or download the dimensions for the 3/4 inch build.
Well, my 27 millimeter cutters arrived, and so I was able to complete the bore hole drillings on the two 1/4 inch thick hardboard wheels. I'll show this process from layout to completion in case anyone else would like to do a small build. I purchased a 2-foot by 2 foot piece of 1/4 inch thick hardboard at Home Depot, which worked out nicely. The panel was actually about 1/4 inch larger in both dimensions, and as I would be able to cut four 12-inch wheels from the panel, I decided to go with 12 inch circular wheels. The dodecagon wheel diameter for a 3 inch build was figured at 46.5 inches, so proportionately the 3/4 inch build would call for an 11.625 inch diameter. I could have built to that specification, but chose to go with 12 inches as it will only make the build more stable, since each pipe will have more wheel surface to lay upon. Here's a photo showing the means that I used for laying out the circles and their radian lines.
The circle scriiber is a Stanley Fatmax Chisel Compass, and works far better than an ordinary compass for drawing circles this size or larger.
The True Angle layout tool is a 23 inch model and allows for very accurate angle settings and scribing of the radian lines. Since two wheels are used for this build, the radian lines are scribed 60 degrees apart, and when assembled on an axle the wheels will be rotated for a 30 degree separation.
In the photo below, you can see that I scribed another smaller circle upon the wheel. The radius for this circle is 4.5 inches to be in proportion to build specs. The bore holes for the pipes will be centered where the smaller circle intersects the radian lines. I cut out the 12 inch wheels with a saber saw as I didn't have a jig saw available, which I would have preferred using. The idea is to cut close to the 12 inch circle's pencil mark without cutting into the mark. Next, I drilled a 1/8 inch hole at the wheel's center and followed that up with a 1/4 inch hole so that I could attach and secure a 1/4 x 3 inch round head stove bolt. Starting with the smaller drill allows for better accuracy in following the mark left by the chisel point compass. This allowed me to insert the bolt in a a drill chuck and spin the wheel so that I could true it by applying a sanding block to the perimeter as it rotated.
After truing the wheel, the last step was to drill the 27 millimeter bore holes which the pipes must pass through. I used an awl point to accurately make a depression at the centers where the smaller circle intersects the radian lines, and passed a 1/8 inch drill bit through those centers using my bench-top drill press. I then mounted the 27mm cutter in the drill chuck and carefully lined up the cutter's 1/4 inch center drill with each of the 1/8 inch holes. Here's what each of the completed wheels look like.
The work on the wheels is now completed, except that the center holes must be enlarged to accept the 3/8 inch x 6 inch shaft. To place the wheels the desired 1.250 inch distance apart, and lock them to the shaft so that they are set 30 degrees apart in rotation, I will be using shaft collars. The collars are attached to the shaft with set screws to lock them in place, and I will use a small drill to bore a hole through the side of each collar that will also pass through each wheel when in proper alignment. That will allow me to insert a small screw to lock the wheels to the collars. Two more collars will be placed further out towards the ends of the shafts, and these will be used to maintain the rotational plane at the center of the holding device. I haven't drawn up any plans yet for the holding device, but in my mind it would appear to be a wood block used as the base, with support arms extending upwards from the sides of the block. Nothing extravagant - just simple and supportive. The next step now is to assemble the pipes and fittings up to the 90 degree elbows, attach the short pipes to the elbows, pass these through the bore holes in the wheels, and secure the end caps. Since the elbows and end caps allow the pipe to be inserted 3/4 inch until it bottoms out, and since the wheels are 1/4 inch thick, this means that the short pipes which pass through the bore holes should be no more than 1.750 inches long. I prefer to actually finish them to slightly less than that so that when the end caps are cemented in place they will tightly sandwich the wheel surface between the end caps and the elbows so as to avoid any sideways play as the water sloshes about.
Here's a link where you can read or download the dimensions for the 3/4 inch build.
Comment