Originally posted by Marso Green
View Post
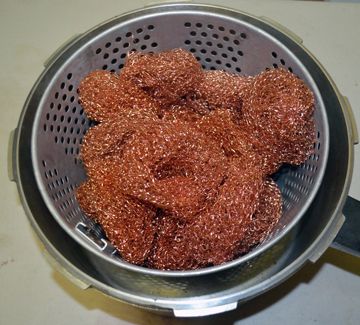
Originally posted by Marso Green
View Post
On the other hand, an air-to-liquid heat exchanger would be very useful for cooling your cooling water so that you can recirculate it.
Originally posted by joan27
View Post
Originally posted by joan27
View Post
Originally posted by joan27
View Post
Originally posted by joan27
View Post
Comment