Hello Qvision,
Hello Qvision,
That is a good Choice, simpler Machine, yet, very powerful...
In My Opinion (IMO):
IF, Before you even start taking apart your original motor...you start "assuming/theorizing/believing" that a Motor that I have displayed here a while back, that I have displayed so many angle interactions and explanations... and that has been replicated by so many people here...AND that BEFORE THAT...I have wounded hundreds of this Motors, in all sizes and "colors"...thinking something is wrong with it?...To me that is a "daring attitude" without the right knowledge...but to You... it would be an obstacle to "see" your Future Asymmetric Motor running properly...other words, and also simpler..."You will be programming yourself for failure..."...Ok?
WRONG ASSUMPTION WITHOUT EVEN A REAL TEST.
It is very obvious You HAVE NOT Analyzed this Design Model properly...
Take a look at the size of Brushes, their WIDTH, compared to the size of Commutator Elements ANGLES of INTERACTION (And I have displayed "pretty big sized" brushes here)
THEN, You will notice, the brush size is "Approximate" One Third here...of the whole comm element...
Now go back to your "Assumption" and ALL those "Common Time Sweep" for Two simultaneous Coils or Transition Time...and calculate Interaction Time...based on say...3600 RPM's (taking it "easy"...knowing this Motors go higher than that)...
If We have Three divided by 360º...every element is "Approximate" @ 120º (knowing we have a gap in between, disregarding it here for being too small)...right?...OK, So...One Third of 120º is 40 degrees right?...So, divide that by two Commutator Elements on each side between center of brush...what we got then?...20º to turn off one coil and go full on second one...
Calculate "Transition Time" here...at 3600 RPM's...then DO IT for 20,000 RPM's...
You will see what I have written many , many times BACK...It is completely worthless to consider such "Action"...MUCH LESS...To assume they are "so equal" they will ALL cancel to ZERO.
IMO?...What Do I think of this?
I will tell you...
Ignorance is DARING...
An old phrase that I love...AND VERY TRUE
Regards
Ufopolitics
PD: And Please, a Message to All:
ALL Motors and Interaction Related Posts, let's keep them together in the other Asymmetric Machines Thread.
It will be of much more easier access for new coming members or anyone to have all related Material in just one Thread...and not be scattered all over...
Originally posted by qvision
View Post
i've decided to try with a 3-pole motor due to it's simplicity and just to observe the difference in behaviour between that and a standard motor :
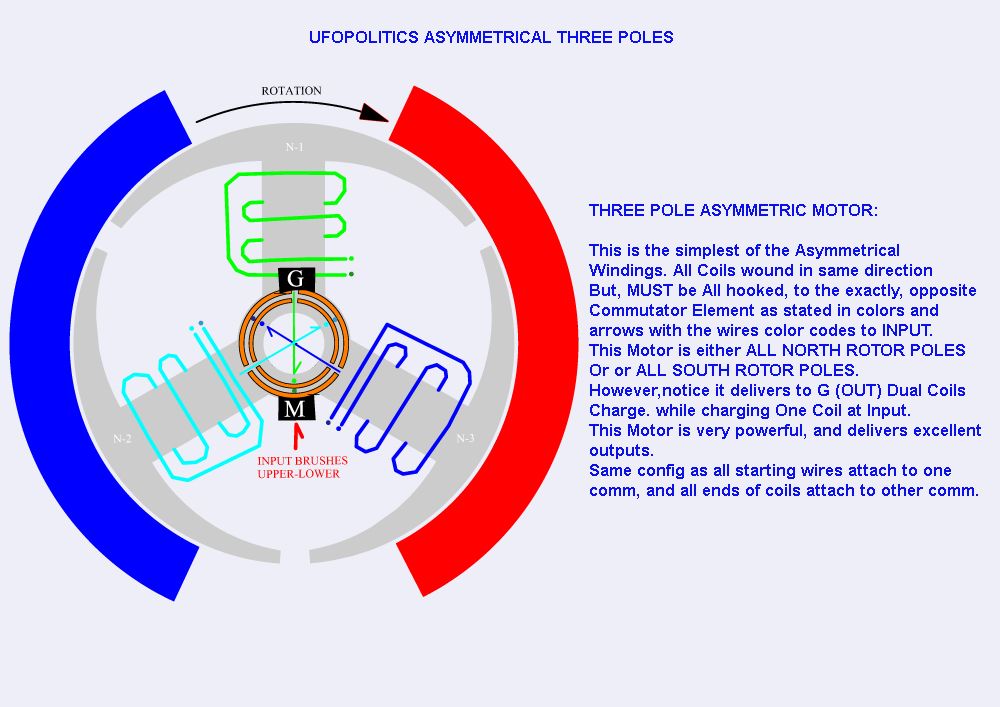

One thing is confusing me and i would like to clear it up before i start work on this.
In the description above it says the advantage of this winding is that there are two coils outputting and only one coil inputing.
I've analysed the firing sequence of the coils and this seems to be wrong.
In the description above it says the advantage of this winding is that there are two coils outputting and only one coil inputing.
I've analysed the firing sequence of the coils and this seems to be wrong.
IF, Before you even start taking apart your original motor...you start "assuming/theorizing/believing" that a Motor that I have displayed here a while back, that I have displayed so many angle interactions and explanations... and that has been replicated by so many people here...AND that BEFORE THAT...I have wounded hundreds of this Motors, in all sizes and "colors"...thinking something is wrong with it?...To me that is a "daring attitude" without the right knowledge...but to You... it would be an obstacle to "see" your Future Asymmetric Motor running properly...other words, and also simpler..."You will be programming yourself for failure..."...Ok?
Using the coil colours in the diagram (Gree, Blue and Turqoise) the input firing sequence is :
Green.
Green and Turq.
Turq.
Blue and Turq.
Blue.
Green and blue.
In the list of input charges above, the coils not on each line are obviously outputting.
When you analyse the sequence you can see that the input and output charges balance out, they sum to zero.
Green.
Green and Turq.
Turq.
Blue and Turq.
Blue.
Green and blue.
In the list of input charges above, the coils not on each line are obviously outputting.
When you analyse the sequence you can see that the input and output charges balance out, they sum to zero.
WRONG ASSUMPTION WITHOUT EVEN A REAL TEST.
It is very obvious You HAVE NOT Analyzed this Design Model properly...
Take a look at the size of Brushes, their WIDTH, compared to the size of Commutator Elements ANGLES of INTERACTION (And I have displayed "pretty big sized" brushes here)
THEN, You will notice, the brush size is "Approximate" One Third here...of the whole comm element...
Now go back to your "Assumption" and ALL those "Common Time Sweep" for Two simultaneous Coils or Transition Time...and calculate Interaction Time...based on say...3600 RPM's (taking it "easy"...knowing this Motors go higher than that)...
If We have Three divided by 360º...every element is "Approximate" @ 120º (knowing we have a gap in between, disregarding it here for being too small)...right?...OK, So...One Third of 120º is 40 degrees right?...So, divide that by two Commutator Elements on each side between center of brush...what we got then?...20º to turn off one coil and go full on second one...
Calculate "Transition Time" here...at 3600 RPM's...then DO IT for 20,000 RPM's...
You will see what I have written many , many times BACK...It is completely worthless to consider such "Action"...MUCH LESS...To assume they are "so equal" they will ALL cancel to ZERO.
What are people's thoughts on this ?
Thank you,
QV.
Thank you,
QV.
I will tell you...
Ignorance is DARING...
An old phrase that I love...AND VERY TRUE

Regards
Ufopolitics
PD: And Please, a Message to All:
ALL Motors and Interaction Related Posts, let's keep them together in the other Asymmetric Machines Thread.
It will be of much more easier access for new coming members or anyone to have all related Material in just one Thread...and not be scattered all over...
Comment