Hi Bizzy, When you do set back up, you might like to try this if you haven't
already tried it. The change is just the two diodes between the battery and cap
and the motor drawing from the cap directly. The result should be that the
capacitor can fluctuate above and below the battery voltage for the amount of
the diode's voltage drop. So for instance if the diodes had a voltage drop of 0.5
volts and the battery was at 12.5 volts the cap could go from 12 to 13 volts
without really affecting the battery. If the cap is big enough then that might be
enough energy to run the machine. 13 volts across a 30000uF capacitor is 2.535 joules
and 12 volts in the same cap is 2.16 joules so there is 0.375 joules to play with
without charging-discharging the battery. I think the principal can be used
by different modes with voltage drop devices of some other nature maybe as
well.
It would be better if the cap didn't go below the battery voltage, but
I can't think of any way to do away with that left diode, maybe two diodes in
series to the battery from the cap would help.
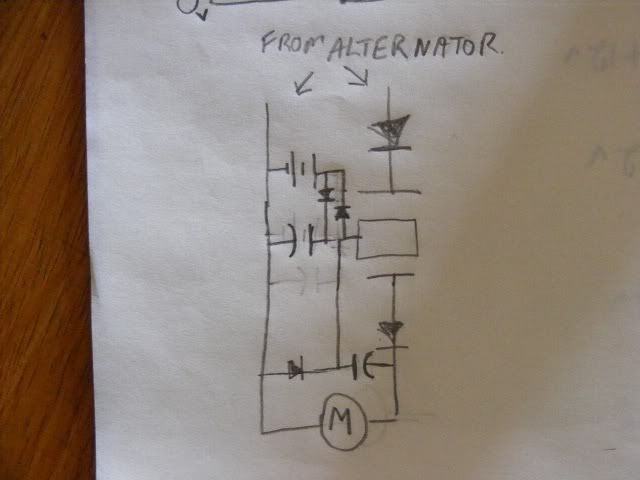
I think I copied the part of your circuit correctly leaving out the alternator
rectifiers. If not I apologize.
Cheers
already tried it. The change is just the two diodes between the battery and cap
and the motor drawing from the cap directly. The result should be that the
capacitor can fluctuate above and below the battery voltage for the amount of
the diode's voltage drop. So for instance if the diodes had a voltage drop of 0.5
volts and the battery was at 12.5 volts the cap could go from 12 to 13 volts
without really affecting the battery. If the cap is big enough then that might be
enough energy to run the machine. 13 volts across a 30000uF capacitor is 2.535 joules
and 12 volts in the same cap is 2.16 joules so there is 0.375 joules to play with
without charging-discharging the battery. I think the principal can be used
by different modes with voltage drop devices of some other nature maybe as
well.

I can't think of any way to do away with that left diode, maybe two diodes in
series to the battery from the cap would help.
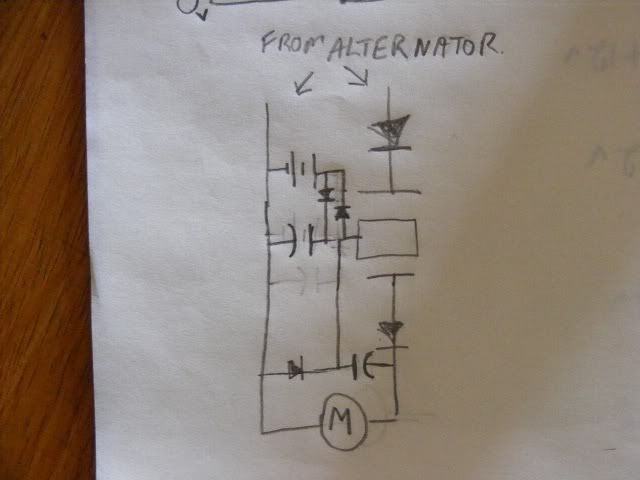
I think I copied the part of your circuit correctly leaving out the alternator
rectifiers. If not I apologize.
Cheers
Comment